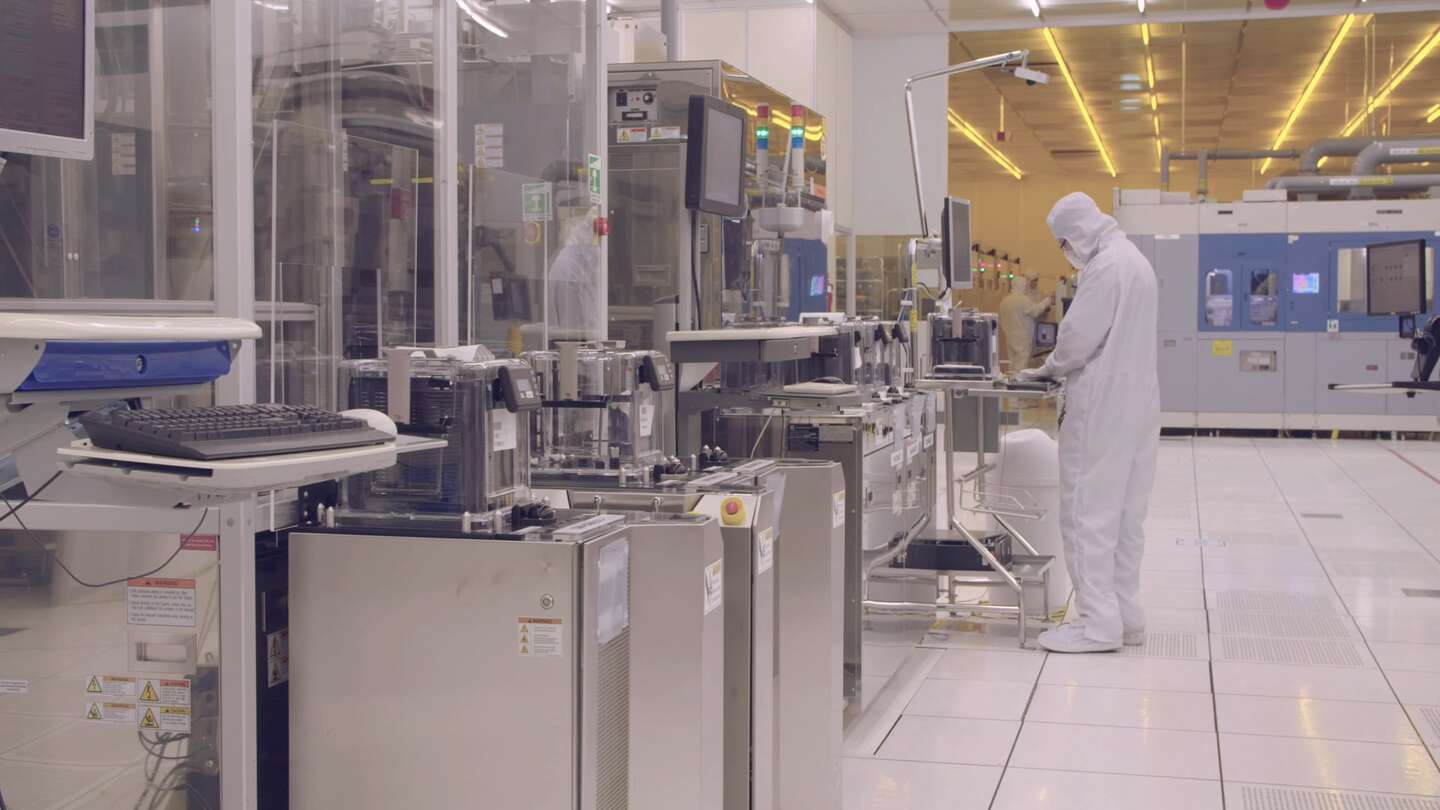

Manufacturing of Embedded HMI Systems
We provide a comprehensive production range of Embedded HMI Systems, catering to both individual prototype production with quantities as low as one unit and large-scale, high-volume mass production of Embedded HMI Touch Screens. As a dedicated system supplier, we are committed to excellence in quality management, ensuring the highest standards are met to guarantee your maximum success. Our expertise spans from the initial concept to the final product, delivering precision and reliability at every stage of the manufacturing process.
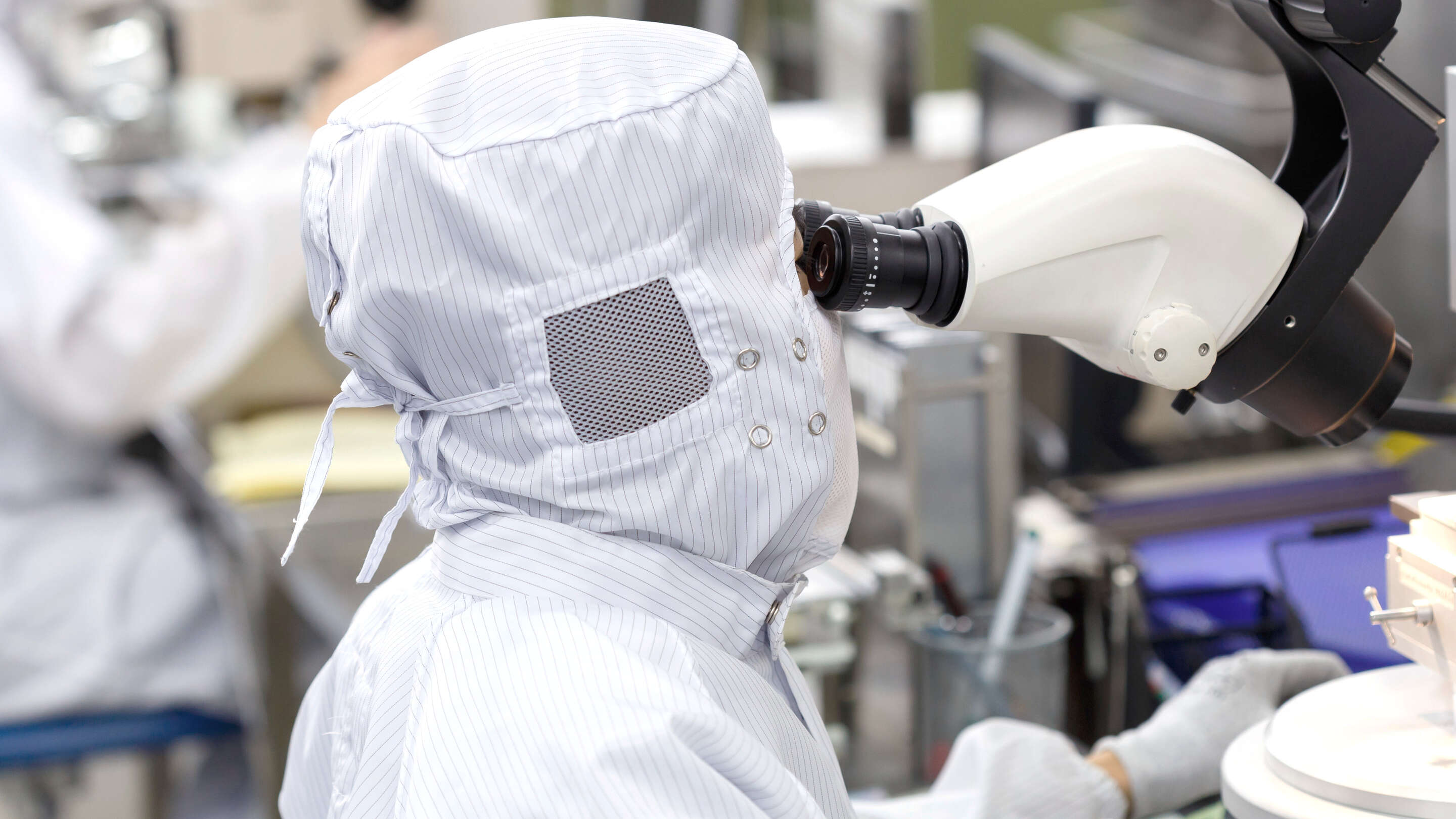
In today’s competitive market, exceptional touchscreen technology requires more than basic manufacturing—it demands precision, innovation, and an unwavering commitment to quality. At Interelectronix, we understand these complexities and use state-of-the-art technology and rigorous testing to produce top-tier touchscreens meeting the highest industry standards. Our advanced production techniques, including in-house rapid prototyping and modern CNC milling, ensure superior quality and efficiency. We excel in adhesive bonds, seals, and finishing processes, guaranteeing unmatched visual clarity and durability. Tailored production methods ensure seamless integration into your applications. Rigorous testing guarantees reliability and compliance with industrial, medical, and military standards. Choose Interelectronix for solutions that exceed expectations, benefiting from our expertise and dedication to excellence. Contact us today to learn more.
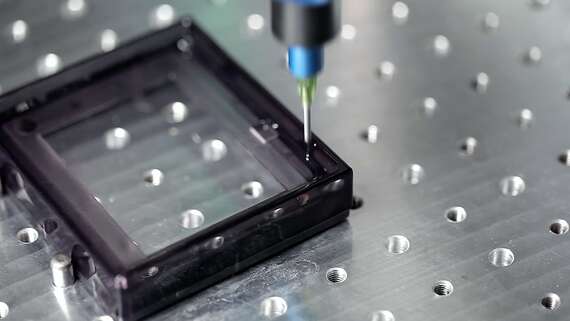
The quality of seals and adhesive joints is crucial for the reliability and durability of touch systems. Meeting application-specific requirements and environmental conditions, along with precise material selection and application, is essential. Interelectronix uses high-quality materials and high-precision dispensers for consistent foam or adhesive application. Plasma cleaning ensures optimal surface preparation, while clean room production prevents contamination. UV curing enhances adhesive performance by providing rapid curing times and improved bonding strength, resulting in durable and robust seals that maintain their integrity under various conditions.
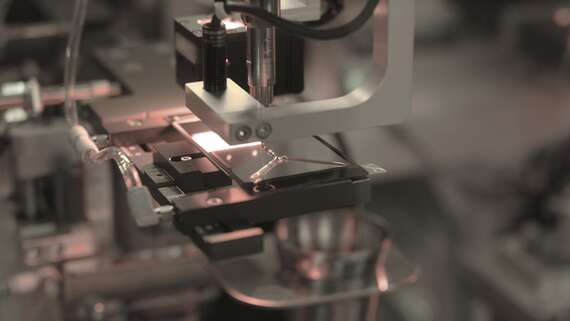
In the optical bonding process, two substrates are seamlessly joined without bubbles using an optical adhesive to ensure superior optical performance. There are two main optical bonding technologies: dry bonding and wet bonding. Dry bonding employs an optical tape to connect the substrates, while wet bonding utilizes Liquid Optically Clear Adhesive (LOCA). The choice between these methods depends on the display size and application. We excel in both techniques, providing high-quality optical bonding at competitive prices.
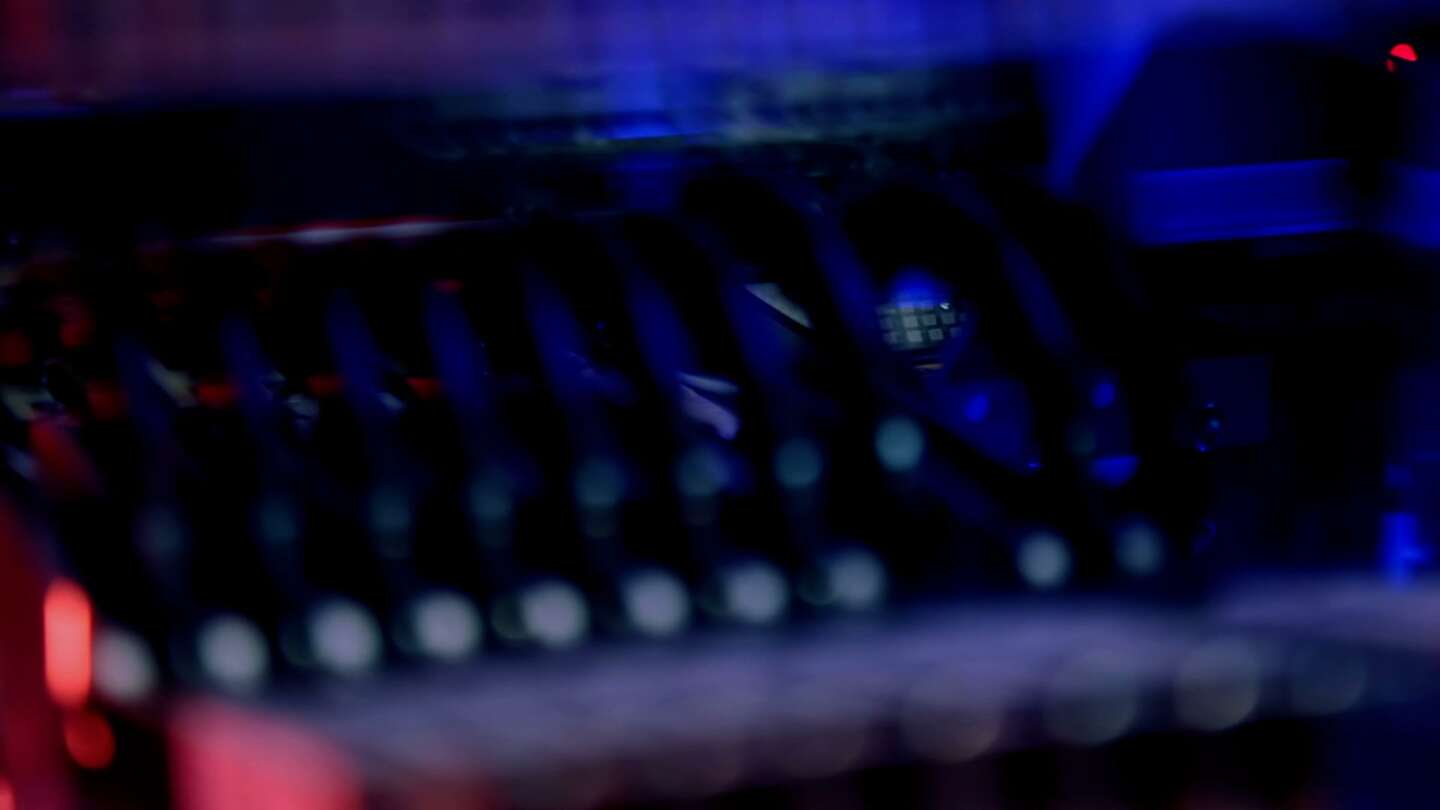

Glass Lamination
At Interelectronix, our expertise in glass lamination ensures exceptional durability and performance for your devices. We specialize in laminating two glass sheets or a glass sheet with a touch sensor, creating seamless, robust interfaces. Our commitment to innovation, advanced technology, and stringent quality control makes us the ideal partner for your touch screen needs. By choosing Interelectronix, you are investing in superior reliability and user experience. Trust us to enhance your devices’ performance. Reach out today to learn more about our solutions.


Cleanroom assembly
We focus on top-quality standards to make our touch screens reliable. Our cleanroom assembly process has strict requirements for the environment, production steps, and equipment, which can be quite demanding. We follow all rules about airborne particles to ensure everything is up to standard. With over 20 years of experience, we are the best choice for making touchscreens in cleanroom settings, ensuring that the optical processes are free from dust and lint, which is essential for top performance.

Foam Gaskets
In-house die-cutting of adhesive tapes and foam gaskets ensures precision for custom shapes and sizes, perfectly fitting specific applications. Our touchscreens feature high-quality sealing systems, offering optimal protection for years. We provide various sealing options, including urethane foam gaskets, Poron gaskets, and IP69K-rated seals, which are highly resistant to dust, chemicals, steam, and high-pressure water. For clean indoor areas, urethane foam is ideal, while neoprene sponges or Poron foam suit portable devices exposed to moisture. For outdoor use, durable silicone-based seals are recommended.

Gasket Dispensing
Our gasket dispensing technology efficiently seals housing covers, protecting electrical parts from moisture, dust, air, and other unwanted materials, enhancing product safety and functionality. This fast, precise process saves time, reduces waste, and accelerates assembly, shortening time to market. Alteams offers high-precision form-in-place gasket application with advanced robotic equipment, ensuring consistent bead profiles for high-volume production. We provide various sealing materials for electromagnetic shielding (EMC) and environmental protection (different IP classes), with three technologies to choose from, tailored to your project’s needs.
